Understanding the Impact of Chinese Injection Molding on Global Manufacturing
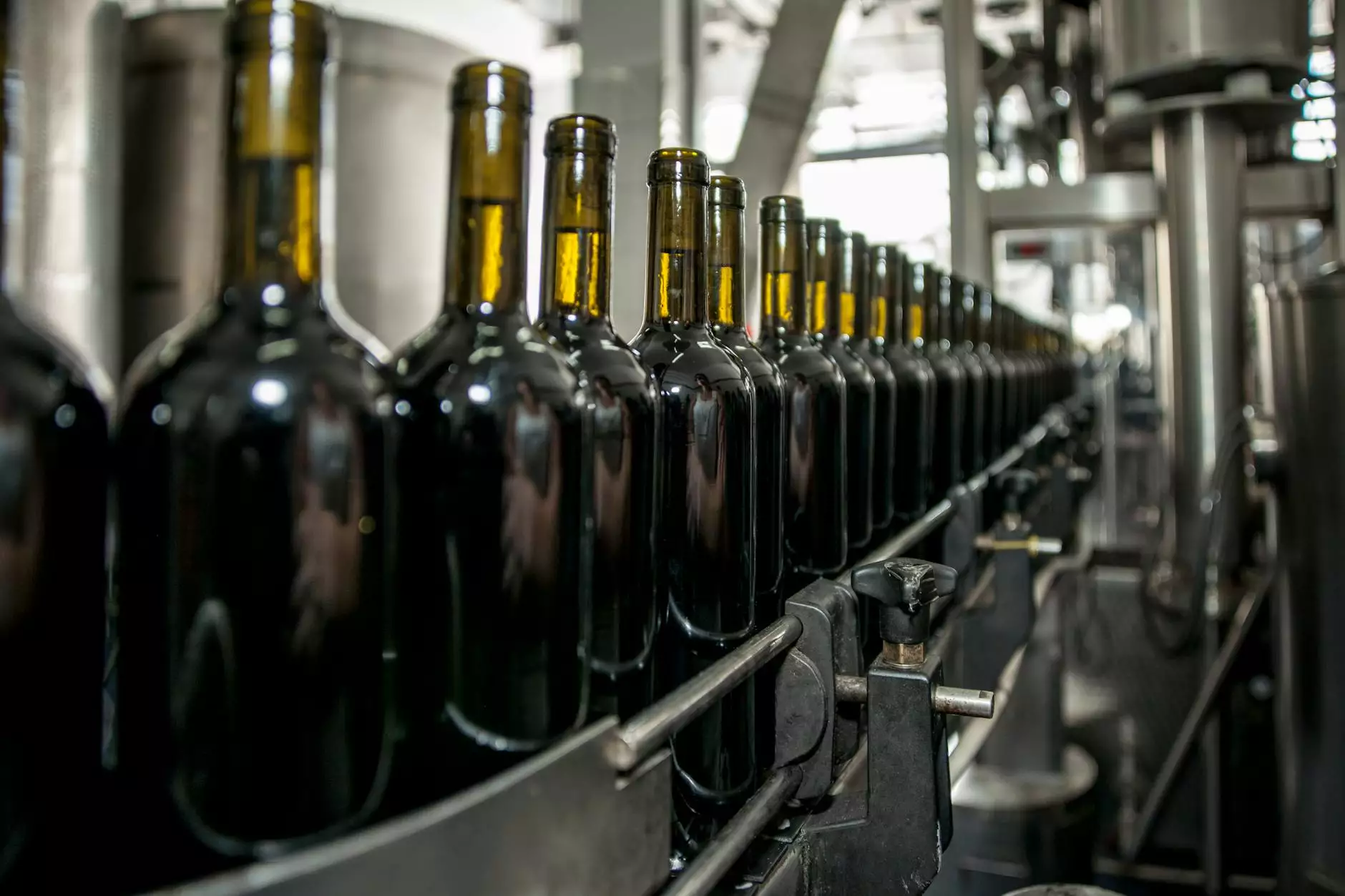
Chinese injection molding has become a cornerstone in the global manufacturing sector, reshaping how businesses approach production and product design. This process, characterized by its high efficiency, versatility, and cost-effectiveness, allows for the mass production of complex and detailed parts with great precision. In this article, we will delve into the intricacies of injection molding in China, explore its benefits, applications, and why it is a preferred choice for many companies around the world.
The Basics of Injection Molding
At its core, injection molding is a manufacturing process where raw plastic is melted and injected into a mold, where it cools and solidifies into the desired shape. This method is particularly advantageous for producing high volumes of the same item, making it ideal for various industries, including automotive, electronics, consumer goods, and more.
How Injection Molding Works
The injection molding process involves several key steps:
- Material Preparation: Raw plastic pellets are first dried and then fed into the injection machine.
- Melting: The pellets are heated in a barrel until they are melted into a viscous liquid.
- Injection: The molten plastic is injected into a pre-prepared mold under high pressure.
- Cooling: The injected plastic cools and solidifies in the mold.
- Mold Opening: Once cooled, the mold is opened to release the finished part.
- Finishing: Any excess material or imperfections are trimmed or smoothed out.
Why Choose Chinese Injection Molding?
When it comes to injection molding, China has distinguished itself as a leading hub for this service, owing to various advantages that make it attractive for businesses worldwide.
1. Cost Effectiveness
One of the most significant benefits of Chinese injection molding is the reduced cost of production. Thanks to lower labor costs and efficient manufacturing processes, companies can save substantial amounts compared to manufacturing in other countries.
2. Advanced Technology
China is home to numerous advanced technology firms that specialize in the latest injection molding machines and processes. The use of state-of-the-art technology ensures that products are manufactured to the highest quality standards.
3. High Production Capacity
Chinese manufacturers can handle large-scale production runs, making them an ideal choice for businesses looking to produce a high volume of products rapidly. This capability ensures timely delivery and helps businesses meet market demand effectively.
4. Versatility in Material Selection
China offers a wide range of materials for injection molding, including thermoplastics, thermosetting plastics, and various composites. This versatility allows companies to choose the material best suited for their products, enhancing functionality and appeal.
5. Extensive Expertise
With decades of experience in the field, Chinese manufacturers have amassed a wealth of knowledge concerning the injection molding process. This expertise contributes to higher quality products and informed decision-making regarding design and materials.
Applications of Chinese Injection Molding
Chinese injection molding has found applications across a plethora of industries. Here are some prominent sectors benefiting from this manufacturing technique:
- Automotive Industry: Manufacturers produce complex parts such as dashboards, bumpers, and interior components with high precision.
- Electronics: Injection molding is extensively used to produce casing and components for smartphones, laptops, and other consumer electronics.
- Medical Devices: The medical industry relies on injection molding for producing syringes, surgical tools, and other intricate devices designed for safety and efficiency.
- Consumer Goods: Everyday products such as containers, toys, and household items are manufactured through injection molding, illustrating its versatility.
Quality Control in Chinese Injection Molding
Quality control is of utmost importance in any manufacturing process, especially in injection molding. Here’s how Chinese manufacturers ensure the highest quality standards:
- Material Testing: Before production begins, materials undergo rigorous testing to ensure they meet specified standards.
- In-Process Monitoring: Throughout the production process, various parameters such as temperature, pressure, and injection speed are continuously monitored.
- Final Inspection: Once the parts are produced, they are inspected for defects, dimensions, and surface finish before shipment.
Design Considerations for Injection Molding
Designing a part for injection molding requires careful planning to optimize manufacturing efficiency and product quality. Here are key considerations:
1. Material Selection
Selecting the right material is vital for ensuring that the final product meets the desired performance criteria. Factors to consider include strength, flexibility, and thermal stability.
2. Wall Thickness
Uniform wall thickness is crucial to avoid warping and ensure even cooling. Parts should be designed with consistent thickness to enhance stability and reduce cycle times.
3. Draft Angles
Incorporating draft angles into designs facilitates easier mold release. A draft angle of 1-3 degrees is generally recommended to prevent damage to the part during removal.
4. Undercuts
Minimizing undercuts in the design can save costs on tooling and production. If undercuts are necessary, consider using sliding cores or lifters in the mold.
Future Trends in Chinese Injection Molding
The future of Chinese injection molding is set to evolve with advancements in technology and sustainability practices:
1. Automation and Industry 4.0
As manufacturers embrace automation, the integration of robotics and smart technology will enhance production efficiency, reduce errors, and lower operational costs.
2. Sustainable Practices
With increasing environmental concerns, the adoption of sustainable materials and practices in injection molding will become more prevalent, promoting eco-friendly manufacturing.
3. Customization and Rapid Prototyping
The demand for customized products and rapid prototyping services is growing. Chinese manufacturers are investing in technologies that enable faster turnaround times for prototypes, allowing companies to innovate more freely.
Why Partner with Deep Mould for Injection Molding?
For businesses seeking comprehensive solutions in Chinese injection molding, Deep Mould stands out as a reliable partner. Here’s why:
- Expertise: Deep Mould has extensive experience in metal fabricators and injection molding processes.
- Quality Assurance: With stringent quality control measures in place, we ensure that all products meet our clients’ specifications.
- Competitive Pricing: Our operational efficiency allows us to offer competitive pricing without compromising quality.
- Customized Solutions: We work closely with clients to develop tailored solutions that address specific needs and requirements.
Conclusion
Chinese injection molding has transformed the landscape of global manufacturing, providing businesses with cost-effective, efficient, and high-quality solutions. Its versatility allows it to cater to multiple industries, and with advancements in technology, sustainability, and customization, its relevance is only set to grow. If you are looking for a trustworthy partner in your manufacturing endeavors, consider reaching out to Deep Mould for unparalleled expertise and service.