Understanding Pressure Die Casting Products
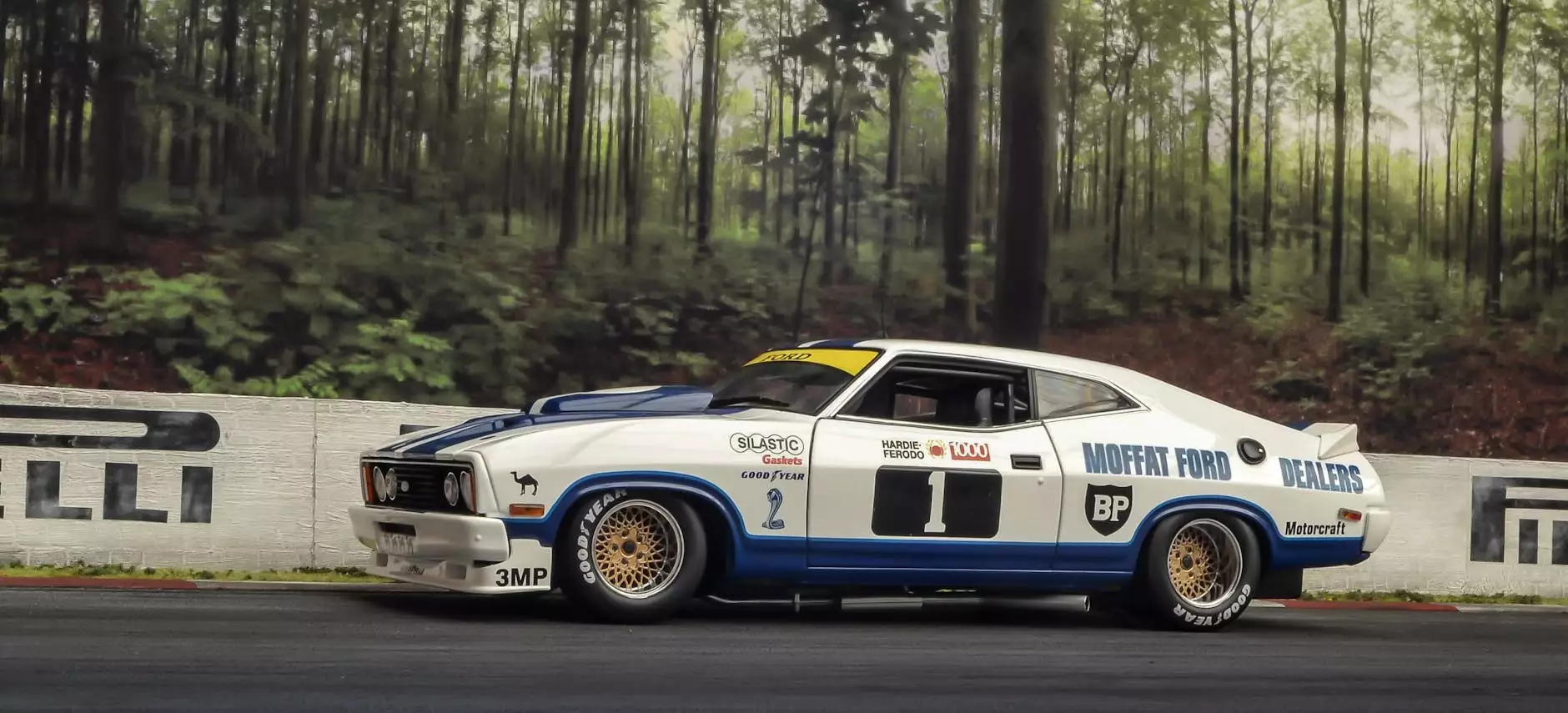
Pressure die casting is a manufacturing process that provides an efficient and cost-effective method for producing high-quality complex-shaped metal parts. The innovative technology involved in this process enables manufacturers to create products that meet the rigorous demands of various industries, leading to increased functionality and improved product lifespan. In this article, we will delve deep into the specifics of pressure die casting products, exploring their applications, advantages, and the future outlook of this essential manufacturing technique.
What is Pressure Die Casting?
Pressure die casting involves forcing molten metal into a mold cavity under high pressure. This not only allows for precise dimensions and a smooth finish but also facilitates the mass production of intricate designs. The types of metals typically used in this process include aluminum, zinc, and magnesium, each offering unique properties suited for specific applications.
The Process of Pressure Die Casting
- Preparation of the Mold: The process begins with the creation of a mold, typically made from steel, which can withstand high pressure and temperature.
- Melting the Metal: The chosen metal is then melted in a furnace, reaching its liquid state at high temperatures.
- Injection: The molten metal is injected into the mold at high velocity and under pressure, filling the voids quickly to form the desired shape.
- Cooling and Solidification: Once injected, the metal cools and solidifies within the mold, taking on its final shape.
- Mold Removal: After solidification, the mold is opened, and the newly formed die-cast part is removed.
- Finishing Processes: Finally, any additional finishing processes, such as machining, polishing, or surface treatment may be applied to enhance the product's appearance and performance.
Benefits of Pressure Die Casting Products
Utilizing pressure die casting products offers numerous benefits that make them an attractive choice for manufacturers across various industries. Here are some of the key advantages:
- High Dimensional Accuracy: The pressure casting process ensures that components are produced to precise specifications, reducing the need for extensive machining.
- Complex Geometry: Designers are not restricted by the limitations of traditional machining methods; intricate shapes can be achieved with ease.
- Improved Mechanical Properties: Products made from die casting possess excellent mechanical strengths, making them suitable for demanding applications.
- Low Production Costs: Compared to other manufacturing processes, pressure die casting is economical, particularly in high-volume production runs.
- Reduced Material Waste: The process optimally utilizes metal, resulting in less scrap and lower environmental impact.
- Enhanced Surface Finish: The final product often requires minimal finishing, thanks to the smooth surfaces produced during the casting process.
Applications of Pressure Die Casting Products
The versatility of pressure die casting products translates into widespread applications across various sectors, including:
Automotive Industry
The automotive sector is one of the largest users of pressure die casting. Components such as engine blocks, transmission cases, and various interior and exterior trims are commonly manufactured using this process, benefiting from the strength and weight reduction characteristics of die-cast aluminum.
Electronics
Aluminum die casting is frequently employed in electronics to produce housings, brackets, and heat sinks due to its excellent thermal conductivity and lightweight properties, making it ideal for electronic applications.
Aerospace
The aerospace sector demands parts that are both lightweight and robust. Pressure die casting provides the necessary characteristics where tolerances are critical, such as in aircraft components and engine casings.
Household Appliances
Many everyday household appliances utilize pressure die casting for their components. Items such as fans, mixers, and ovens often feature die-cast aluminum parts for their reliability and durability.
Choosing the Right Partner for Your Pressure Die Casting Needs
When considering pressure die casting products, selecting the right manufacturer is paramount. Here are some critical factors to consider:
Experience and Expertise
A partner with extensive experience in die casting will have refined their processes, ensuring consistency and quality. Look for companies with a robust portfolio and a proven track record.
Technology and Equipment
The best manufacturers continually invest in state-of-the-art equipment and technology. Advanced machinery can significantly improve efficiency and the quality of products.
Quality Control Measures
An effective quality control process is vital. Ensure that your chosen manufacturer conducts thorough testing and inspections at various stages of the production process to guarantee defect-free products.
Customized Solutions
Every project is unique; thus, it is important that your manufacturing partner can provide tailored solutions that meet your specific design and functionality requirements.
The Future of Pressure Die Casting Products
The future of pressure die casting products looks promising as advancements in technology and materials continue to progress. Key trends to watch include:
- Automation: The integration of automation and smart manufacturing practices will enhance operational efficiency and drive down costs.
- 3D Printing: Combining traditional pressure die casting with 3D printing may open up new avenues for creating complex designs without the constraints of conventional mold manufacturing.
- Sustainable Practices: As industries become more conscious of their environmental impact, manufacturers are focusing on adopting sustainable materials and processes to minimize their carbon footprint.
- Advanced Materials: The ongoing development of new alloys and metal compositions will expand the capabilities and applications of current die casting technologies.
Conclusion
As we have explored, pressure die casting products provide immense value through their precision, cost-effectiveness, and versatility across diverse applications. With a firm grasp of the process, benefits, and future trends of pressure die casting, businesses can position themselves to harness this technology effectively to meet their manufacturing needs. By choosing the right partner, such as DeepMould, companies can innovate their product lines while upholding standards of quality and efficiency, ultimately gaining a competitive edge in today’s fast-paced market.